DEM Simulation model of Conductivity and Calibration in Liggghts
Engineerdo presents an exploration into DEM simulations incorporating thermal modeling, utilizing LIGGGHTS. This method for parameter calibration, designed to bridge simulation and real-world data, is applicable across various DEM software. The focus is on simulating heat conductivity processes, such as a cooling screw for particles.
In such a system, particles move along a cold wall, transferring heat from the bulk material to the wall. The heat dissipation depends on particle conductivity and their motion within the machine. For instance, a well-mixed system transfers heat more efficiently than a stationary one. Thus, simulating particle motion alongside heat transfer is critical.
A key parameter is the heat transfer coefficient between particles. This value cannot be directly adopted from literature due to:
- Variations in grain size distribution in simulations, which alter contact surfaces and affect heat transfer.
- Variability in bulk material properties, such as grain size distribution and density, requiring empirical measurements.
Experiment Overview
To accurately represent the bulk material’s thermal behavior, experiments must measure its heat conductivity. Subsequently, simulation parameters are adjusted to match experimental data, a process termed calibration.
The experimental setup involves a sand-filled beaker in boiling water. Play sand serves as the bulk material. Temperature sensors are positioned to measure water temperature, the wall temperature near the sand, and the temperature at the center of the sand. Heat transfer dynamics are tracked, as rising temperatures propagate from the wall sensor to the center sensor over time.
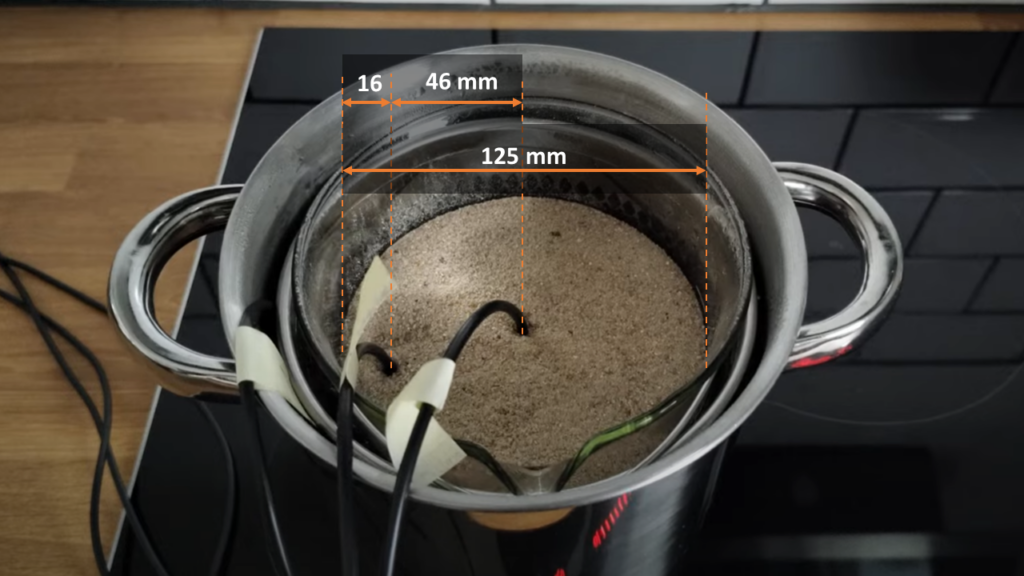
Although seemingly simple, such measurements often demand expensive equipment, including platinum sensors and data loggers. To overcome this, a cost-effective, user-friendly measurement system was developed, eliminating the need for costly components.
Innovative Measurement System
This modular system records three temperatures simultaneously using basic hardware and software. Sensors are strategically placed in water and sand, with their positions measured for simulation compatibility. Measurements typically span 45 minutes.
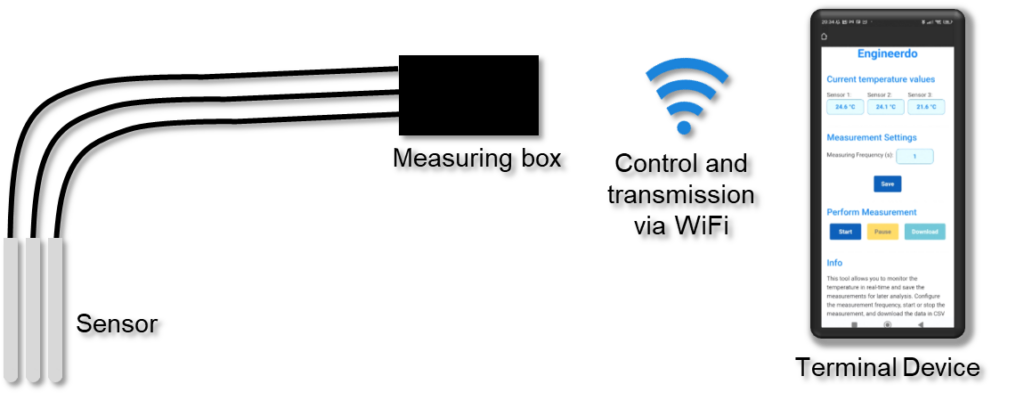
The system connects via USB for power and includes Wi-Fi functionality. Data acquisition is managed through a simple web interface, accessible via a PC or smartphone. Results are downloaded as CSV files for analysis, often using spreadsheet software.
A prototype of this Wi-Fi-enabled temperature sensor, designed to simplify thermal measurements, is showcased on the Engineerdo website, detailing its specifications and development progress.
Calibration in LIGGGHTS
Calibration begins by setting up a thermal model in LIGGGHTS that mirrors the experimental setup, including geometry, sand properties, and boundary conditions.
The thermal calibration script is available here. Key adjustments include defining thermal capacity and conductivity parameters, aligning the simulation’s temperature curve with experimental data. Initial particle temperatures and thermal boundary conditions are specified, with results visualized in ParaView.
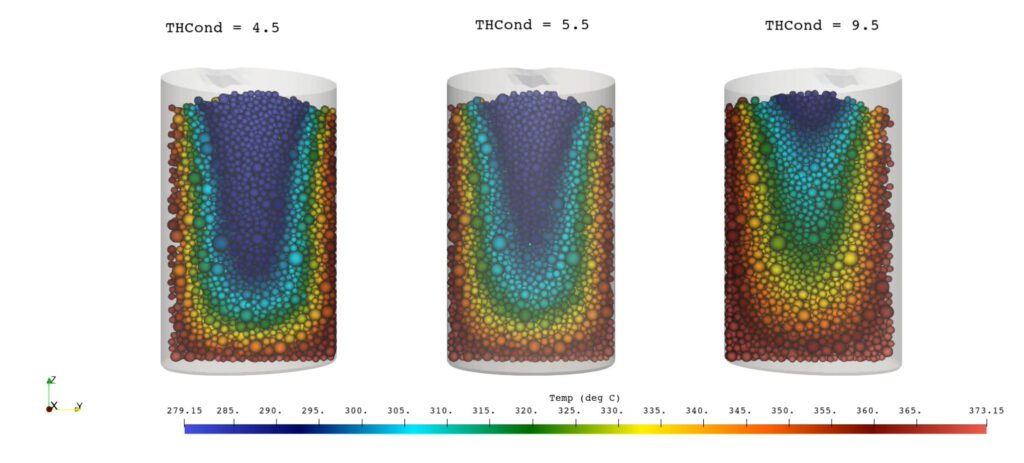
By iteratively adjusting thermal conductivity, the simulation aligns with experimental temperature profiles. For standard materials like sand, thermal capacity can often be referenced from literature, while specialized materials require direct measurement. Validation is achieved through consistent results from multiple sensors.
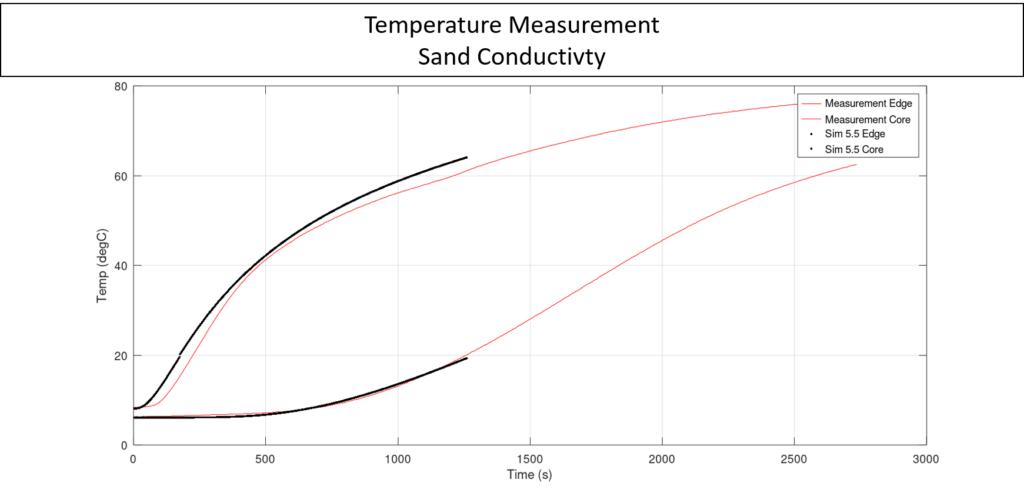
Results and Insights
Once calibrated, the simulation offers valuable insights into heat transfer dynamics in granular materials. Applications extend to industrial drying processes and thermal studies of geological formations.
Conclusion
This guide demonstrates the calibration of DEM simulations using real-world thermal data. The approach integrates experimental validation with simulation accuracy, offering a robust tool for engineering and research. For further inquiries or feedback, visit Engineerdo and explore additional resources on the topic.